S series PET Preform injection moulding machine
PET bottle preform Injection machine large shot but economic price
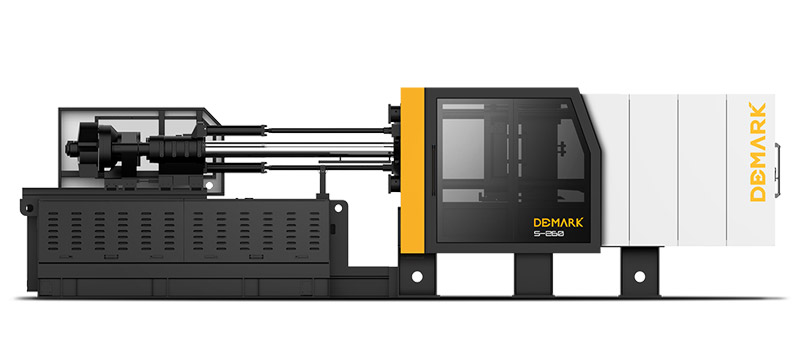
Our S series preform injection machine specialises in the PET bottle preform, based on only preform products charater to develop the total injection system, in big differene with other normal injection machine. With Demark precision preform injection molds, advanced servo hydraulic system, temperature control system, post cooling take out robot, plasticzation & injection, clamping unit and ejection unit, the S series injection machine will brings you more returns with limited investment.
Video (S300-72Cavity-10g)
Technology
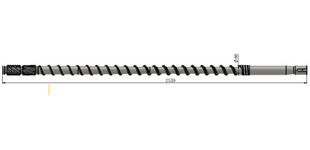
High efficient plasticization
Based on the rich knowledge of bottle preform production, Demark choose the special screw with LD ratio at : and with barrier thread structure which could signficantly increase the plasticization efficiency. A 260T PET preform injection machine could work with 80mm screw, which is suitable for PET preform production.
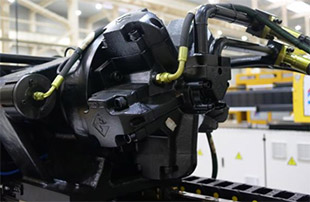
STAFFA hydraulic motor
More torque need when the screw work with PET material because of its high viscosity. Demark choose UK brand STAFFA hydraulic motor which has lower rotational speed but higher torque.
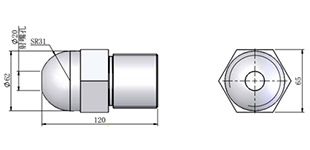
Bigger nozzle
The S series PET bottles injection machine with a 20mm nozzle size which could inject more material at one time and reduce the injection time. But the nozzle on normal machine at the same tonnage usually less than 10mm which has a longer injection time.
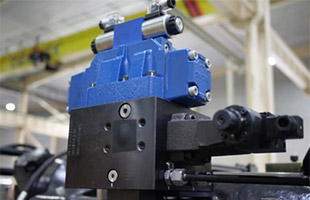
Back pressure controlled by proportional valve
The back pressure controlled by proportional valve which can controlled on the HMI screen.
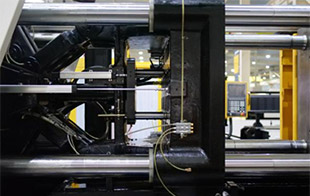
Bigger injection but small clamping
Since the projected area of preform is not very big thus less clamping force need in the prefrom production. The small clamping unit means less energy consumption on moveing the palten and less area need to put the bottle preform injection molding machine.
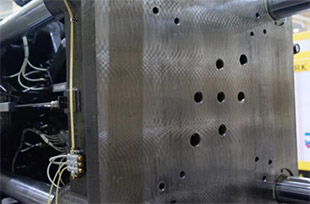
High rigidity platen and higher compatibility
We increase the thickness and strength of the platen to ecsure the stable movement and reliability.
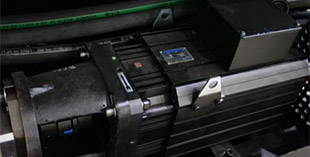
Mold open and eject synchronization (optional)
By equiping extra one set of servo motor and oil pump, the mold open and ejection could happen at the same time which could reduce cycle time up to 2 seconds.
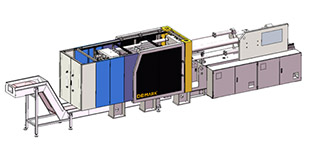
Preform conveyor
No oil ciruit under the injection base which can equip with conveyer under the clamping unit. The design save area, automatic transfer and looks good. But the normal injection machine usually equip the conveyor in the front of the safety door which is blocking the operator to see the machine and need more area alse looks bad.
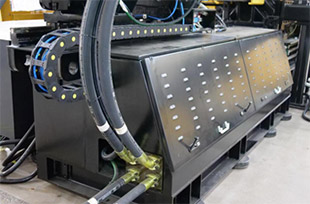
Motor power
The motor power is much bigger than the normal injection machine at the same toonage which because the high viscosity of PET material and needs more power to drive the screw to ensure the efficiency of plasticization. Excellent oil circuit design and brandly oil valve make the injection, platen movement and ejector faster and more precise. The servo motor and oil pump is designed to put outside which makes easy maintenance.
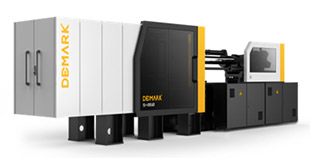
Excellent cycle time
S300/2500 as example, 48 cavities, 15g water preform, cycle time 15s. Comparing: normal machine 20s.
S260/2000 as example, 24 cavities, 36g water preform, cycke time 20s. Comparing: normal machine 30s.
Excellent integration ability
-
The excellent integration ability in industry, including drying system, chiller, air compressor. We have a great relationship with those companies and provide less delivery time even lower price comparing on the market.
-
We choose or customized the auxiliary with more experience than normal injection machine company. For example, the preform production need lots of chilled water so the normal chiller is not big enough to meet this demand. Usually Demark customized the chiller with bigger water pump from our supplier which ensure enough water flow and chilling efficiency.
-
Demark responsible for the whole system not including the preform injection machine but also the mold and auxiliaries. Comparing with normal injection company who only focus on its injection machine, customer will find it very difficult to solve even any small problem that need cooperation between injection machine company and other supplier.
Main technical features
Item | Unit | S260 / 1500 | S260 / 2000 | S300 / 2000 | S300 / 2500 |
Screw L/D Ration | L/D | 25 | 25 | 25 | 25 |
Screw Diameter | mm | 75 | 80 | 80 | 90 |
Injection pressure | kgf/cm² | 1280 | 1125 | 1400 | 1106 |
Injection volume | cm³ | 1414 | 1608 | 1810 | 2290 |
Shot weight (PET) | g | 1654 | 1882 | 2117 | 2680 |
Shot weight | oz | 58 | 66 | 75 | 95 |
Clamping force | T | 260 | 260 | 300 | 300 |
Clamping Stroke | mm | 540 | 540 | 585 | 585 |
Max/Min Thickness of mold | mm | 200 - 580 | 200 - 580 | 300 - 720 | 300 - 720 |
Space Between Tie Bars (W*H) | mm | 570 * 570 | 570 * 570 | 660 * 760 | 660 * 760 |
Ejector Stroke | mm | 150 | 150 | 180 | 180 |
Ejector Force | T | 8 | 8 | 20 | 20 |
NO.of Ejector Pins | pcs | 5 | 5 | 5 | 5 |
Max system pressure | kg/cm² | 160 | 160 | 160 | 160 |
Motor Power | kw | 36 | 36 | 44 | 44 |
Heater Input Capacity | kw | 32 | 36 | 36 | 44 |
Machine Size (L*W*H) | cm | 700 * 200 * 220 | 7000 * 160 * 220 | 800 * 200 * 220 | 800 * 210 * 220 |
Machine Weight | T | 12 | 12 | 14 | 14 |
Notice: Demark reserve the rights to make any product improvement or specification change without prior notice.
|
Main technical features
Item | ECO260 / 2000 | ECO260 / 2500 | ECO300 / 2500 | ECO300 / 3500 |
Preform weight | Cavity | Cavity | Cavity | Cavity |
15g | 32 | 32 | 48 | 72 |
45g | 24 | 32 | 32 | 48 |
65g | 16 | 24 | 24 | 32 |
100g | 8 | 12 | 16 | 24 |
260g | 4 | 6 | 6 | 8 |
Notice: The views expressed are my own and do not necessarily represent the views of DEMARK.
Copyright © 2013 - 2024 www.pet-machinery.com all rights reserved. Designed by Tina | Sitemap